Tapping into Learning: FlexArm Keeps the Fun in Fabrication
- Jim Wahl
- Jun 4, 2018
- 4 min read
(Wapakoneta, OH) – More than many machinists, Charlie Shaw can arguably reason that his work helps make happy, smart children. Shaw is the president of CW Shaw, a fabrication shop for science center exhibits. Shaw and his team manufacture the larger than life contraptions that children of all ages interact with, cranking, turning, pulling and pressing while subtly learning about problem solving, math and natural science.
Seeing photos of children learning and laughing while using his products is rewarding, especially since he knows that machining those exhibits is no laughing matter. From concept to construction and installation, C.W. Shaw handles the fabrication, millwork, metalwork and electronics of large-scale exhibit projects.
Shaw has a machine shop and CNC machine center on site, and has a considerable array of tools—he never knows what unique demands the next project will bring. Two years ago, an addition to the tool bench streamlined how Shaw taps holes in stainless steel, a very common material that comprises the majority of exhibits that come through the shop.
The Ball Range
The project was a Ball Range for a science center in Fort Lauderdale, Florida. Visitors at the exhibit experiment with force and trajectory by aiming a nozzle and shooting balls at targets. The exhibit features two stations: one where visitors create air pressure through a plunger, and a second where participants aim and shoot the balls. At 50 feet long, the sizable length of the range encourages participants to use teamwork as they help the shooter adjust to get balls through the hoops.
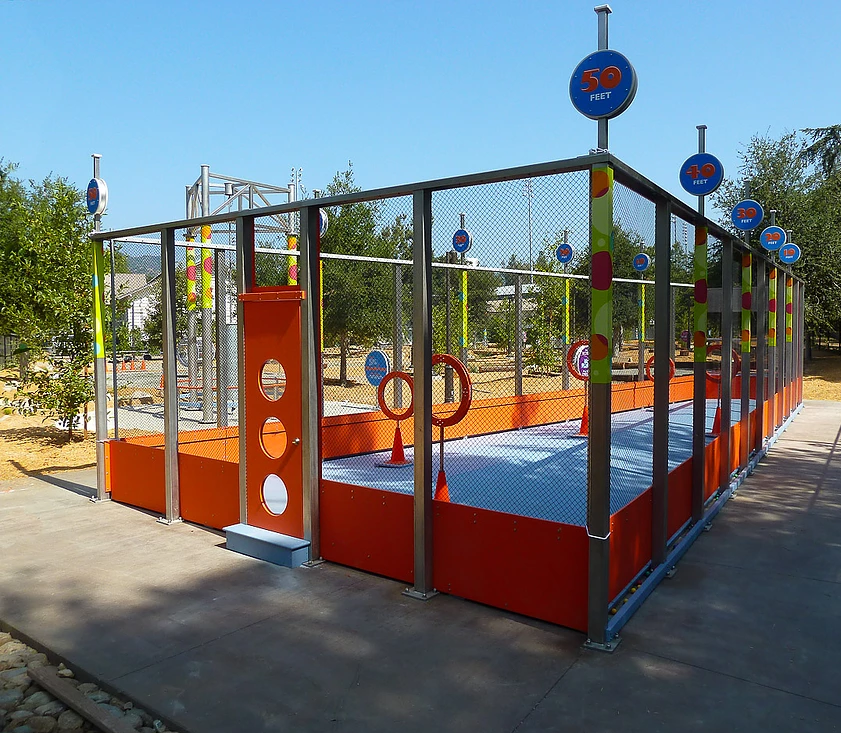
The project was straightforward, and Shaw had already built a similar exhibit for a museum in Pasadena, California. The California model was engineered to withstand an earthquake by using 11-guage, 1” square 304 stainless steel tubing. The project demanded upwards of 1,000 1/4” holes, which Shaw’s crew tapped by hand with a cordless drill—laborious, to be sure, but not out of the normal for the shop.
The Fort Lauderdale model, however, needed to be built to withstand 156-mile-per-hour winds, the top speed of a Category 4 hurricane. Shaw’s engineers designed the model with 1/4” wall 4” square 304 tubing. Suddenly the 1,000 holes posed a problem: a cordless drill would surely break multiple taps, and could risk scrapping the piece being tapped.
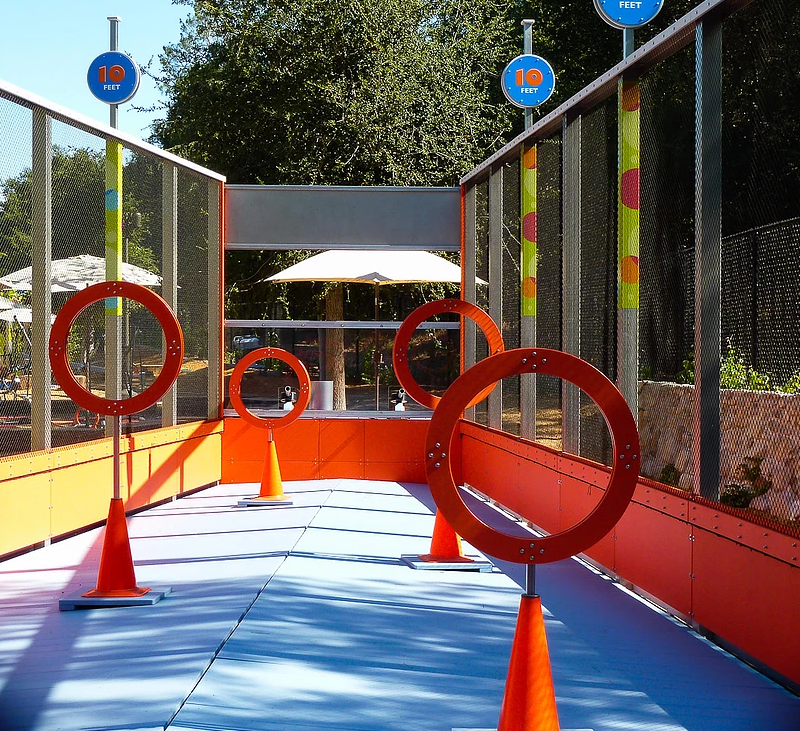
Scrapping a piece of material already worth $500 and which took hours of machining to produce because your operator broke a bit while tapping the thousandth hole is a waste of money, material and precious production time. After researching on the internet, Shaw reached out to FlexArm Inc. FlexArm manufactures hydraulic and pneumatic tapping arm solutions and Shaw suspected a mounted tapping arm could handle the project. He purchased a GH-18 electric tapping arm with a tilt head and steel stand.
Tapping, Not Scrapping
FlexArm tapping arms are designed to make tapping easy and quick. Adjustable gas counter-balanced springs allow an operator to position the tap over a hole without straining or fatigue. The tool absorbs the torque created by the motor, increasing tap accuracy. The GH-18 model has a 110v green power motor with #6-5/8” tap capacity.

An adjustable torque clutch allows the tap to stop turning when it encounters any obstruction that might cause breakage, significantly reducing the likelihood of breaking a tap. A CNC machine averages a broken tap ever 300 holes, whereas a FlexArm can go 3,000 holes without breaking a tap.
Breaking a tap in a CNC machine means the part has to be removed, repaired, and deindexed, as some of the original datums may have been machined away. Operators also have to edit the program code to continue machining from the exact right step. Of course, this is all assuming you can keep the part and not scrap it.
Even at an initial cost in the ballpark of $5,000, Shaw’s FlexArm paid for itself in the first job. Tapping ¼’’ holes in 1/8’’ steel is a lot easier than tapping ¼’’ hole in ¼’’ material. When you approach a 1x1 aspect ratio, the likelihood of breaking a tap skyrockets, particularly in 304-grade stainless steel, he explained. When the material is closer to ½’’ you’d need a FlexArm or EDM machine to even get the broken taps out. Even after the thousandth hole, the FlexArm didn’t break a single tap, and the $500 components were saved from the scrap heap.

While some pieces are still best tapped in the VMC, Shaw found an unexpected use for the FlexArm in pieces that don’t fit in the machining center or pieces that demand exacting precision. Shaw was pleasantly surprised recently how easy it was to tap holes in his welding table for special fixtures.
As for working with FlexArm, Shaw noted, you don’t know how it is to work with until you have a problem. Initially, FlexArm sent C.W. Shaw the wrong model, but worked quickly to remedy the error.
“Even through the error, which could have been the dealer’s fault, they were great to work with” Shaw said.
Putting the Fun Back in Fabrication
There’s no doubt Charlie Shaw has a fun job. He and his team build exhibits that capture children’s imagination and sense of fun, while subtly teaching them skills and facts about the natural world. When it comes down to machining some of those exhibits, the job gets a little less fun. Broken taps scrapping expensive material and causing costly production downtime are a buzz kill.
The FlexArm puts a little of the fun back into production by decreasing the likelihood of tap breakage, and making the tapping process easy and efficient. Shaw doesn’t use the FlexArm on every project that comes into his shop, since projects change so drastically from one to the next.
For large scale projects, or projects that demand precision, the FlexArm allows Shaw to bid with confidence. One broken tap can suck all the profit out of a project—which can suck all of the fun out of the job. On a recent project that involved over 4,000 holes for a bed of nails designed to teach children about pressure distribution, the FlexArm helped make production a little less like…well, laying on a bed of nails.
The bed of nails demo, created by CW Shaw for the Arizona Science Center was recently featured on Ellen.
Comments