Hours Saved in the Pursuit for Perfection
- Lindsay Eilerman
- Jul 13, 2017
- 3 min read
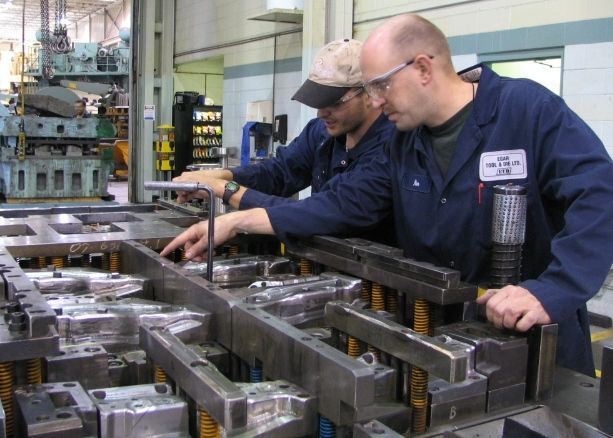
Manufacturing: It’s not all grunt production. Die grinding is hard work, yet it borders on sheer artistry.
Die grinding takes a great deal of determination, focus and control. It is a skill that takes patience and care; based on precision and attention to detail.

We considered the process when we walked into a stamping plant the other day. It was a typical factory setting with lots of rugged activity taking place, including life-sized dies and man-sized parts going through the die grinding process – by hand. What does this involve? The die grinder operator uses a hand die grinder to chisel down the excess weld bead to a desired surface that is uniform, smooth and free of nicks and burrs. Typically a hand grinder is used to maintain control. If the operator allows too much to remain or go too deep the whole pieces becomes waste – the whole, expensive, time-consuming piece.
In this particular plant, one die can weigh 15,000 lbs. If there is a chip or a blemish – major or minor – it must be welded to fill in the damage. Then the finish must be smoothed. No problem! Just pick up and use one of those hand grinders.....
The solution is not as simple as that. There’s a challenge with using a hand grinder for this purpose – it must remain
perfectly perpendicular for a seamless finish. A series of stones are used to buff out the weld, much like you would do with sandpaper. Smooth it down until it is as smooth as a baby's bottom.
That’s the goal. Baby-bottom buffed.
We walked in to the production area and saw one piece – one life-size, extra-large-man-size piece of metal being finished by hand with a die grinder. It was a beautiful sight – artistry in motion. Die grinding artistry. Very slow motion. The outcome was gorgeous – as it slooooooooooowly unfolded in front of us. We watched the intense fortitude of the die grinder operator, knowing there were hours and hours of focused concentration ahead as he slowly worked around the piece with the hand grinder.
We were surrounded by parts in production: quarter panels, doors, car hoods, trunk lids. There were stamping areas, each the size of a room, where two dies are stamped together into a mold. If the die gets a blemish, that the 15,000 lb part has to come out of the mold to be worked on. It literally can take hours just to remove the part.
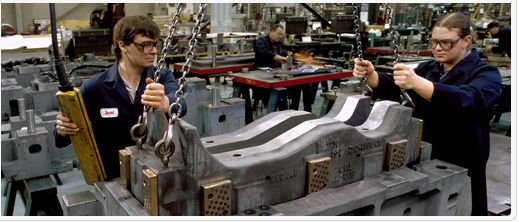
We’re talking big jobs. We’re talking a lot of time involved.
We like to say: We have an arm for that.
We did. With us. In a box.
We opened our box and set up the contents: a FlexArm Die Grinder. We magnetized the arm directly to a mold still on the line. Eyes in the room grew wide as we showed them the carbide tip, deburring tool, perpendicular and consistently quality results. We raised the carbide point of the die grinding tool up to the side of the metal and….
Turned on the motor.
Ran the tip on the edge.
A few sparks flew as the sound of ohhh and ahhhrose from onlookers. As the carbide tip rolled and polished we could almost hear the sound of applause rising from the ranks which was overshadowed by the reality of the voice that proclaimed:
"That would have taken us a day and a half by hand… And it took you 30 minutes!"
Our shoulders didn’t hurt. Our hands weren’t numb. Our arms still had feeling in them. And after 30 minutes, we could look forward to getting more multiple man-sized pieces smooth and clean, with no chance of waste because the carbide tip did the work, the arm maintained the control, and all the operator does is hold the tool and enjoy the ride.
Comentarios